Um unterschiedliche Systeme untereinander zu vernetzen, bedarf es Lösungen, die auf einer breiten Basis aufbauen.
Klaus Rupprecht, kaufmännischer Direktor der SYS TEC electronic GmbH, erläuterte der TREND-REPORT-Redaktion, warum heterogene Ansätze ins Nirwana führen und welche Auswege existieren.
Herr Rupprecht, welchen Stellenwert nehmen freie Hardware (OS-Hardware) und Open-Source-Software im Kontext der Entwicklung des IoT ein?
Aus unserer Erfahrung müssen die Einstiegshürden zu konkreten Lösungsansätzen so niedrig wie möglich gehalten werden. Dies gilt technisch genauso wie kommerziell. Bevor eine Investitionsentscheidung in Richtung IoT getätigt wird, werden in der Regel Pilotanlagen installiert, um a praxi den Nutzwert begreif- und kalkulierbar zu machen. Somit ist die Verwendung von offenen Standards in Hard- und Software ein probates Mittel, um die Kosten und die Erstellungsdauer für Pilotanlagen niedrig zu halten.
Ein weiterer, nicht zu vernachlässigender Aspekt ist für mich, den Wissens- und Erfahrungshorizont von jungen, angehenden Ingenieuren urbar zu machen. An den Hochschulen werden diese quasi mit den offenen Standards groß. Somit wäre es töricht, diesen vorhandenen und durchaus wertvollen Schatz nicht auch in professionellen Lösungen zur Anwendung zu bringen. Die Qualität der offenen Standards hat sich meines Erachtens auch dadurch stark verbessert, dass nicht mehr nur ambitionierte Hobbyisten diese für private Applikationen verwenden, sondern auch sehr professionelle Entwicklergruppen ihre Ergebnisse publizieren und somit die Standards sowohl in der Breite als auch in funktionalen Details beachtenswert sind.
Grundsätzlich sehen wir uns als Systemintegrator in der Pflicht, die offenen Standards für unsere Industriekunden vor Einsatz auf Herz und Nieren zu prüfen. Die meisten Kundenapplikationen bestehen in der Regel somit aus einer Mischung von offenen Standards gepaart mit sehr veritablen Komponenten, die von Spezialisten für Spezialisten entworfen und vermarket werden.
Wie können heute Bestandsmaschinen am besten nachgerüstet werden?
Um Bestandsmaschinen in die IoT-Welt zu überführen, braucht es heterogene und minimalinvasive Lösungen. Minimalinvasiv meint dabei im Besonderen, dass wir zum Beispiel an einer Produktionsmaschine, die jeden Tag sicher ihren Dienst verrichtet, keine Komponente installieren, die die Verfügbarkeit der Maschine negativ beeinflusst. Es ist erkennbar, dass die Zeitfenster zur Installation von zusätzlichen Komponenten während des Produktionsablaufes knapp bemessen sind. Zudem kann eine Veränderung an der Maschine möglicherweise den Verlust von Gewährleitungsansprüchen gegenüber dem Maschinenlieferanten darstellen.
„Es ist sehr interessant, dass es oftmals in der technischen Welt Entwicklungen gibt, die offenbar ihrer Zeit vorauseilen.“
Für einen Teil unserer Kunden ist eine Nachrüstung dann akzeptabel, wenn wir ein paralleles System installieren, das nicht in die originäre Steuerungssoftware und damit in die Abläufe eingreifen kann. Wir bieten zudem batteriegetriebene Sensoren an, die noch nicht einmal einen Anschluss an die Versorgung der Maschine benötigen, was gleichbedeutend ist mit der Tatsache, dass wir in der Regel ohne zusätzliche Kabelinstallation auskommen.
Diese Lösungen sind sehr individuell auf die jeweilige Maschine projektiert und bieten auch Zugang zu Messwerten, die mit der Steuerung der Anlage bisher nicht erfasst werden konnten. Wir sehen hier insbesondere Anwendungsfälle von vorausschauender Wartung von Verschleißteilen an schnell drehenden Teilen einer Maschine. Kurz und knapp: Wie wäre es, eine permanente Überwachung für Achslager auf etwaige Frühausfälle zu installieren?
Erwähnenswert ist in diesem Zusammenhang, dass wir die IoT-Daten über separate Übertragungskanäle senden können. IT-Verantwortliche fordern meist, den Zutritt zu Shopfloor-Daten nur über besondere Gateways zuzulassen und vom Datenfluss zum Server (Cloud) strikt zu trennen. Der eingangs erwähnte heterogene Lösungsansatz ist der Tatsache geschuldet, dass ebenso eine technische Möglichkeit angeboten werden muss, die direkt auf die Daten der Maschinensteuerung zugreift. Hierzu ist Expertise notwendig, wie die unterschiedlichen Steuerungshersteller Zugriff auf Daten zulassen. Wir ergänzen in diesem Fall unsere Geräte um eine Art Treibersoftware, die individualisiert mit der Anlage kommuniziert. Ob der Vielzahl von Herstellern und Modellen eine echte Herausforderung, derer wir uns mit Komponenten aus unserem Partnernetzwerk gerne stellen. Wir sehen, die eine optimale Anbindung von Bestandsmaschinen gibt es nicht, obschon wir mit unserem Ökosystem die Installation eines parallelen Systems präferieren würden.
Welche offenen Standards und Austauschformate gibt es?
Es ist sehr interessant, dass es oftmals in der technischen Welt Entwicklungen gibt, die offenbar ihrer Zeit vorauseilen. So ein Beispiel ist für mich das MQTT-Protokoll, das bereits 1999 definiert wurde und das nun in der heutigen IoT-Ära ein anerkanntes Austauschformat für Sensor-to-Cloud-Anbindungen ist. Dass derlei Technologien bereits älteren Ursprungs sind, ist insofern auch eine triviale Erkenntnis. Referenziert man die heutigen IoT-Lösungen auf Machine-to-Machine(M2M)-Kommunikation der letzten 20 Jahre, stellen wir fest, dass die heutige Digitalisierung meist auf einer logischen Weiterentwicklung von etablierten Bestandteilen beruht.
Wirklich neu ist für mich die Kombination von verschiedenen Hardware- und Softwaretechnologien zu IoT- oder besser IIoT-Lösungen. Größter Treiber für die IoT-Welt ist nach wie vor die Entwicklung und Verbreitung von Smartphones. Die Infrastrukturelemente, die bedingt durch die Masse der schlauen Telefone heute zur Verfügung stehen, waren vor zwei Dekaden noch undenkbar und eine Datenübertragung über Provider eine kostenintensive Mühsal.
MQTT („Message Queuing Telemetry Transport“) ist ein offenes Nachrichtenprotokoll, das von den meisten Cloudanbietern unterstützt wird. Als Client-Server-Protokoll senden die Clients an den Server Nachrichten mit einem sogenannten Topic. Die Clients abonnieren ergo Informationen, die dann von dem Server (mit Verwendung eines sogenannten Brokers) an die interessierten Clients weitergegeben werden. Da MQTT in der Breite über TCP benutzt wird, können klassische Ethernet-Übertragungskanäle genutzt werden. Sensor-to-Cloud-Kommunikation ist mit der Verwendung von MQTT robust im industriellen Umfeld nutzbar.
Unser Ökosystem arbeitet mit diesem Protokoll, insbesondere zwischen Sensoren und der Instanz Edge-Controller. Wir sehen zudem einen enormen Vorteil darin, dass die Clients hardwareunabhängig sind, also nahezu jedes heute verfügbare Endgerät (Smartphone, Tablett, PC … ) verwendet werden kann, auch in beliebigen Kombinationen untereinander. Aus unserer Sicht bleiben die klassischen Feldbus-Protokolle wie zum Beispiel Profibus und CANopen noch lange erhalten; lediglich könnte sich der Trend zur Verwendung von Ethernet-basierter Hardware weiter verstärken, sind doch durch Verwendung dieser Physik fast alle gängigen Protokolle übertragbar, bis hin zu echtzeitfähiger Datenübertragung von kritischen Messstellen.
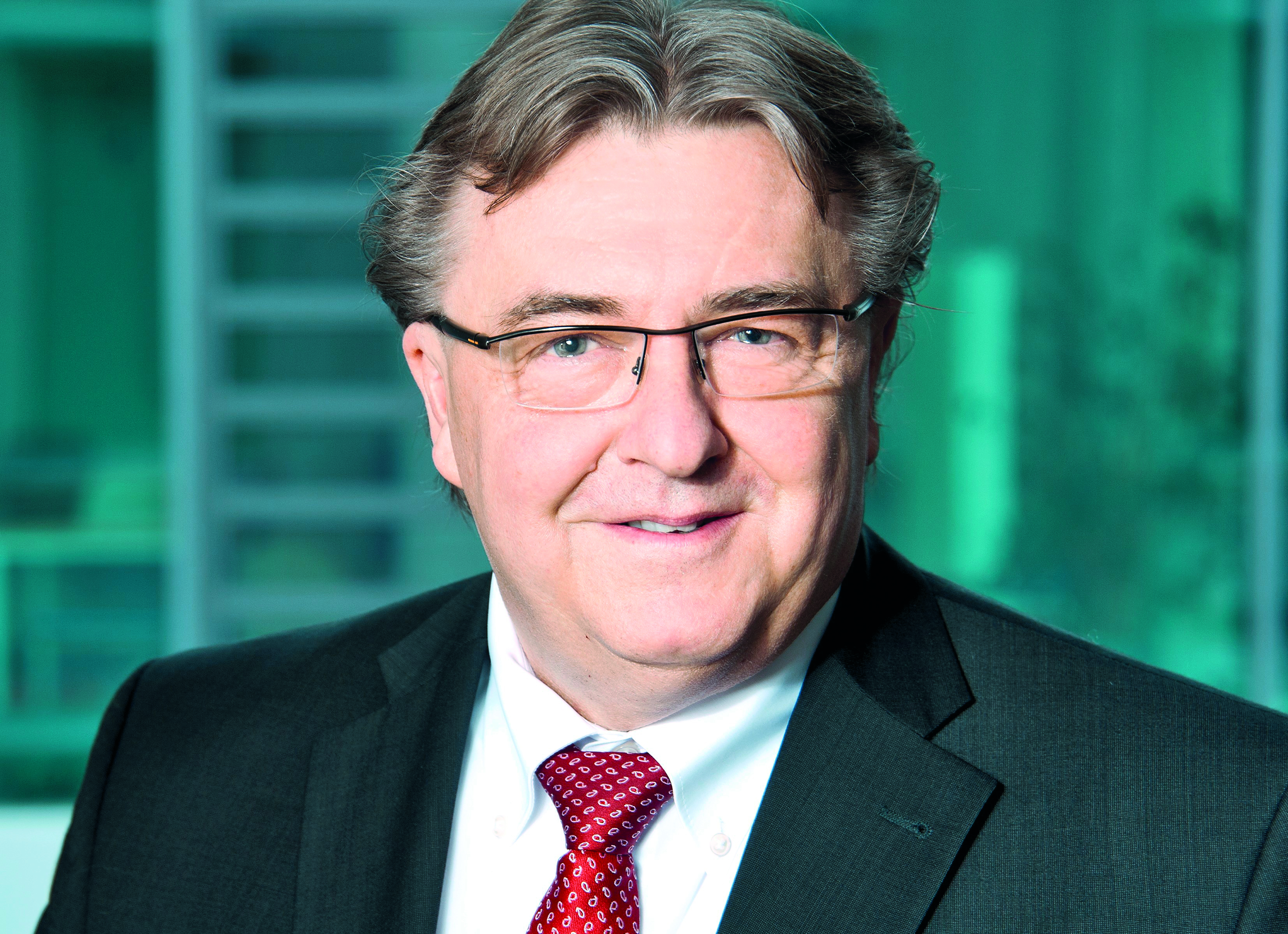
Was kann mit dem offenen Standard OPC UA erreicht werden und sehen Sie noch weitere sich etablierende Standards?
OPC UA ist wie MQTT ein Beispiel einer ausgereiften, guten technischen Basis, die jetzt ihren Weg in die Applikationen findet. Ebenfalls im Zeitalter der M2M-Kommunikation geboren, wächst sich OPC UA zu einer wichtigen Schlüsselkomponente aus. Im Zentrum dabei steht die Aufgabe, Kommunikationsprotokolle zu definieren und zu verwenden, die branchenneutral und hardwareunabhängig arbeiten. Bereits 2013 wurde in einer Umfrage zur „Plattform Industrie 4.0“ (Quelle: Forschungsunion, Acatech 2013) die Standardisierung als größte Herausforderung von Branchenkennern benannt. Daran hat sich nach unserer Meinung nichts geändert.
Die Vernetzung unterschiedlichster Systeme untereinander (z. B. Steuerung zu Steuerung, Steuerung zu Visualisierungsgeräten usw.) führt über firmenspezifische, heterogene Ansätze ins Nirwana, einhergehend mit einer Verschwendung von Ressourcen von kostbaren Software-Entwicklern, von denen es bekanntermaßen zu wenige gibt. Somit ist es nicht verwunderlich, dass immer mehr Firmen der Automatisierungs-Industrie mit OPC-UA-basierten Lösungen aufwarten. Als Mitglied der OPC Foundation haben wir auf unseren Edge-Controllern einen eigenen OPC-UA-Stack implementiert, in erster Linie mit der Funktion, sogenannte HMI („Human Machine Interface“) von Drittanbietern verwenden zu können. Wir planen die Konnektivität Schritt für Schritt zu erweitern und OPC UA als Bindeglied zu Steuerungsgeräten unterschiedlichster Hersteller anzubieten.
Ziel könnte es sein, OPC UA perspektivisch auch bis auf die Sensorebene zu bringen, um Daten von Messstellen direkt aus der Feldebene in die Managementebene oder gar auf den Enterpriselevel zu bringen. Warum sollte nicht auch die ERP-Software direkt Statusinformationen der Maschine bekommen und verarbeiten? Wir sehen hier Vorteile und verbinden heute schon MES-Software-Funktionen mit Zustandsdaten aus der Maschine. Wir überwachen hiermit die Verfügbarkeit unserer Bestückungsanlagen und können im Falle von Störungen schneller reagieren und die gestörte Fertigung sofort neu planen.
Schauen wir uns Anwendungsfelder an, in denen IoT und IIoT besonders großen Nutzen für den Anwender bringen, kommen wir zwangsläufig, lokal betrachtet, auf die Bereiche vor, zwischen und hinter der Produktionsmaschine. Wir sprechen über Logistik und Materialfluss. Überwachen wir unsere Produktionsanlagen perfekt und steigern hier die Verfügbarkeit und damit die Produktivität, ist es doppelt fatal, wenn Material nicht zur rechten Zeit am richtigen Ort ist.
„Viele, sehr gute Funklösungen zur standardisierten Vernetzung kommen von Start-up-Unternehmen aus Finnland – kein Zufall.“
Was liegt also näher, als den Materialfluss zu überwachen durch ein sogenanntes Asset-Tracking-System. Bewegliche Objekte (z. B. Transportkisten) werden lokalisiert auf Ort und Menge. Somit benötigt man Funksignal-Standards, die auf Consumer-Standards wie Bluetooth aufsetzen. Kombiniert man diese Hardware-Standards mit speziellen Software-Stacks, können vermaschte Kommunikationsnetze realisiert werden, die als mobile Knoten untereinander oder übereinander zu einem Gateway kommunizieren. Hier etablieren sich zunehmend spezielle Lösungen zu Standards, sodass es in naher Zukunft möglich sein wird, unterschiedliche Anwendungsfälle mit einer Systemarchitektur zu bearbeiten.
Eine Kombination von Maschinenüberwachung und Asset-Tracking ist heute schon Stand der Technik, eine Kombination mit intelligenten Beleuchtungssystemen innerhalb der Werkhalle ist ebenso denkbar. Auch hierbei hilft uns indirekt die Entwicklung der Smartphones weiter. Viele, sehr gute Funk-Lösungen zur standardisierten Vernetzung kommen von Start-up-Unternehmen aus Finnland – kein Zufall.
Warum benötigt Industrie 4.0 eine semantische Beschreibung von Maschinen- und Produktionsanlagen?
Wie bereits im Zusammenhang der OPC-UA-Technologie erörtert, ist auch hier die Standardisierung die zentrale Herausforderung. Stellen wir uns vor, wir würden keine semantische Beschreibung anstreben. Als Ergebnis wäre der Zoo von eigentlich gleichen Maschinen über die individuelle Darstellung der Hersteller nicht beherrschbar. Somit muss eine generische Beschreibung der Anlagen entstehen, die die Maschine, um am Beispiel der Automationspyramide zu bleiben, in der Management- und Enterpriseebene eindeutig definiert. Schließlich wollen Sie sich nicht mit dem Kauf der Maschine auf einen Anbieter von MES-Software festlegen, nur weil die Schnittstelle individuell gestaltet ist, gleiches gilt für die Anbindung des führenden ERP-Systems.
Aus anderer Blickrichtung würde eine heterogene, nicht harmonisierte Darstellung der Maschinen und Anlagen zu ständigen Anpassungen auf (fast) allen Ebenen der Datenverarbeitung führen. Welche Kosten dies verursachen würde, ist schlecht einschätzbar, könnte allerdings den Nutzen (Einsparung durch Verwendung von IIoT) deutlich runterschmelzen. In diesem Zusammenhang sollte man auch daran denken, dass Maschinen und Anlagen installiert und gewartet werden müssen. Es wäre ein Graus, würden wir in Zukunft weiterhin auf rein manuelle Konfiguration setzen.
Die Instandhaltungs-Abteilungen wären sicher schnell überlastet. Die semantische Beschreibung meint die Vereinheitlichung von Daten. Die Vereinheitlichung oder Harmonisierung der Daten wird sinnvollerweise bereits auf der Komponentenebene einer Maschine oder Anlage durchgeführt. Ähnlich der Funktionsweise der USB-Schnittstelle meldet sich ein Anlagenteil mit einer Beschreibung oder Kennung, die die Software erkennt und zuordnet. „Plug and Play“ hieß es mal in der PC-Welt, heute wandelt sich der Begriff zum Ziel „Plug and Work“.
Neben reinen Parametern, die den Anlagenteil definieren, ist es erstrebenswert, auch die grafische Darstellung von Prozessen zu harmonisieren. Werden die Geometrie- und Topologiedaten des Anlagenteils bereitgestellt, kann unter Verwendung von Software wie AutomationML die entsprechende Visualisierung zur Laufzeit generiert werden. Das heißt, dass sich auf unterschiedlichen HMI-Geräten die Grafik kongruent aufbaut. So essenziell die Aufgabe der semantischen Beschreibung sicher ist, so ist diese nicht leicht umzusetzen und bedarf zentraler Entwicklung. Die Unterstützung des renommierten Instituts Fraunhofer IOSB ist sicher für viele Unternehmen hilfreich. Im Übrigen stammt der Begriff PLUGandWORK aus dieser Quelle. //
Lesen Sie auch: Voll vernetzt für mehr Transparenz und Effizienz
![]() |
Der Text ist unter der Lizenz CC BY-SA 3.0 DE verfügbar. Lizenzbestimmungen: https://creativecommons.org/licenses/by-sa/3.0/de/ |